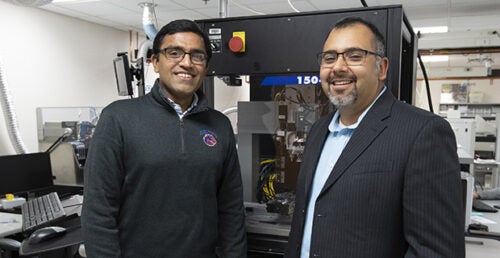
As additive manufacturing is gaining popularity, more people are using some form of printing to manufacture electronics, sensors and more that can be used in everyday items. The technical plans and precision that go into programming and fabricating such everyday items incorporating different functional materials are, in themselves, complex. If the particle size within the inks exceed that of the nozzle opening in the cartridge, the nozzle can easily get clogged. But imagine if the materials could be printed using a nozzle-free approach. That could lead to uninterrupted printing of devices – some smaller than a strand of DNA.
Two Boise State University researchers, in collaboration with the University of Michigan, are working on perfecting just this type of nanomaterial manufacturing process, thanks to a three-year, $427,000 National Science Foundation award.
Boise State principal investigator Harish Subbaraman, an assistant professor of electrical engineering, and David Estrada, an assistant professor of material science and engineering, are working to improve upon current nanomanufacturing technology, which uses highly specialized printers to print nanomaterials that measure as little as one-one billionth of a meter in diameter. The problem is, current printing techniques rely on the use of specialized nozzles to deposit these miniscule materials, and the nozzles routinely clog. The problem becomes more significant when the nozzle diameter is reduced for high-resolution printing, which is increasingly common in the production of biomaterials, sensors and even electronics.
“Say, for instance, you want to print electronics using nanomaterials, or semiconductors that are three atoms thick – or graphene, which is one atom thick. These materials cannot reliably be printed with current state-of-the-art equipment because the nozzle clogs,” Estrada explained. “Our new technique could overcome that.”
The researchers are working to create a nozzle-free manufacturing process, which would eliminate clogs and enable narrower jet streams required for high resolution printing. They are collaborating with University of Michigan Professor Jay Guo, who is developing new hardware to print nanomaterials. The hardware uses a liquid jetting system created by laser-generated focused ultrasound to print various nanostructures. This enables manufacturers to deposit different types, shapes and sizes of nanomaterials on rigid and flexible substances without use of a nozzle.
Subbaraman and Estrada are developing the nanomaterial inks for this new printing system, using specialized equipment purchased through a Department of Energy grant to establish nanoparticle ink synthesis capabilities at Boise State University. They hope to commercialize their inks through a new startup company – INFlex Labs, LLC – resulting from the fundamental discoveries of their Advanced Nanomaterials and Manufacturing Laboratory.
“We’ve printed 10-micron long and a few nanometer diameter carbon nanotubes, which are not possible using current methods,” Subbaraman said. “We’ve demonstrated the feasibility of the approach, now we’re trying to optimize it.”