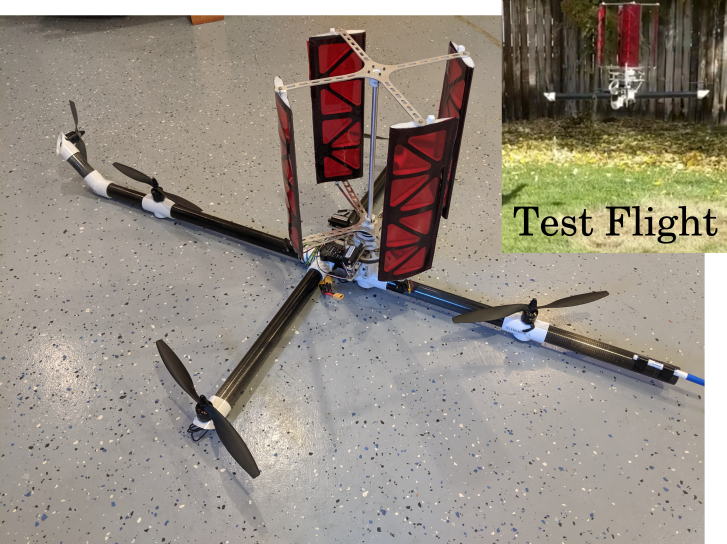
Roads, bridges, hydro-electric dams, wind-turbines – this industrial infrastructure represents significant investments of money, time and effort to maintain. Not only are inspections for many of these structures hazardous, such as those only accessible by rope, but subsurface defects can escape detection by inspectors and go unnoticed until disaster strikes. The dam blows, the bridge collapses: these disasters often come with a terrible human cost.
But what if highly specialized drones equipped with inspection technology could find these hidden defects and remove the need for dangerous and expensive rope-based inspections? With the newly-awarded support of an Idaho Global Entrepreneurial Mission (IGEM) grant for $248,000, two Boise State College of Engineering faculty and Boise-based company Pitch Aeronautics are determined to make that happen, together.
IGEM funds are awarded to Idaho public research universities to partner with industry leaders on research projects geared toward commercialization. This fiscal year, the IGEM Council has awarded $953,711 for research to commercialize innovations that benefit Idaho and beyond.
First, Pitch Aeronautics identified the need for a new kind of drone: a drone with unheard of precision and maneuverability, as well as the ability to touch surfaces to complete inspections.
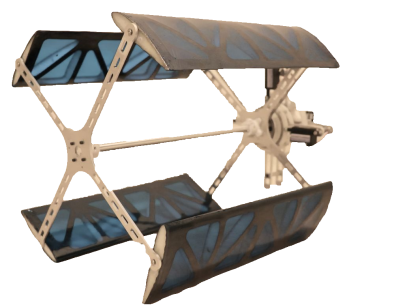
“This drone should reduce the number of times tower climbers have to get up on ropes and ladders to perform inspections,” said Pitch co-founder Zach Adams.
With these parameters, the company then created and patented a drone called the cyclorotor. Unlike conventional drones, the cyclorotor can maneuver gracefully and swiftly to precise locations on infrastructure, such as between the blades of a wind turbine.
“Today’s drones have difficulty in flying close to structures because of the manner in which they move. They must lean forward to move forward and lean back to move back. Leaning takes time and if a gust of wind emerges, they cannot lean fast enough to compensate. Pitch’s drone uses a cyclorotor for lateral control, which allows it to precisely and quickly move forward, backwards or side-to-side without leaning,” Adams explained.
But there was one missing element. Once the drone made its way to its specified location, how would it be able to conduct the inspection for both obvious and hidden flaws?
Associate professor of civil engineering Yang Lu leads the MicroMechanics and Smart Infrastructure Lab at Boise State. In the lab, faculty and student researchers use both computational modeling and experimental measurements to understand, predict and improve infrastructure performance. Lu’s expertise made him the perfect team member to take the cyclorotor’s inspection technology to the next level, and qualify for the IGEM grant that now supports them.
“This IGEM project bolsters the local economy. It aids workforce development by giving engineering students real-world experience; it enhances Idaho economic development, lowers infrastructure assessment costs for state agencies and benefits public safety. We are honored to be a recipient of the innovative IGEM grant and excited for the technical development we can accomplish during this project,” said Lu.
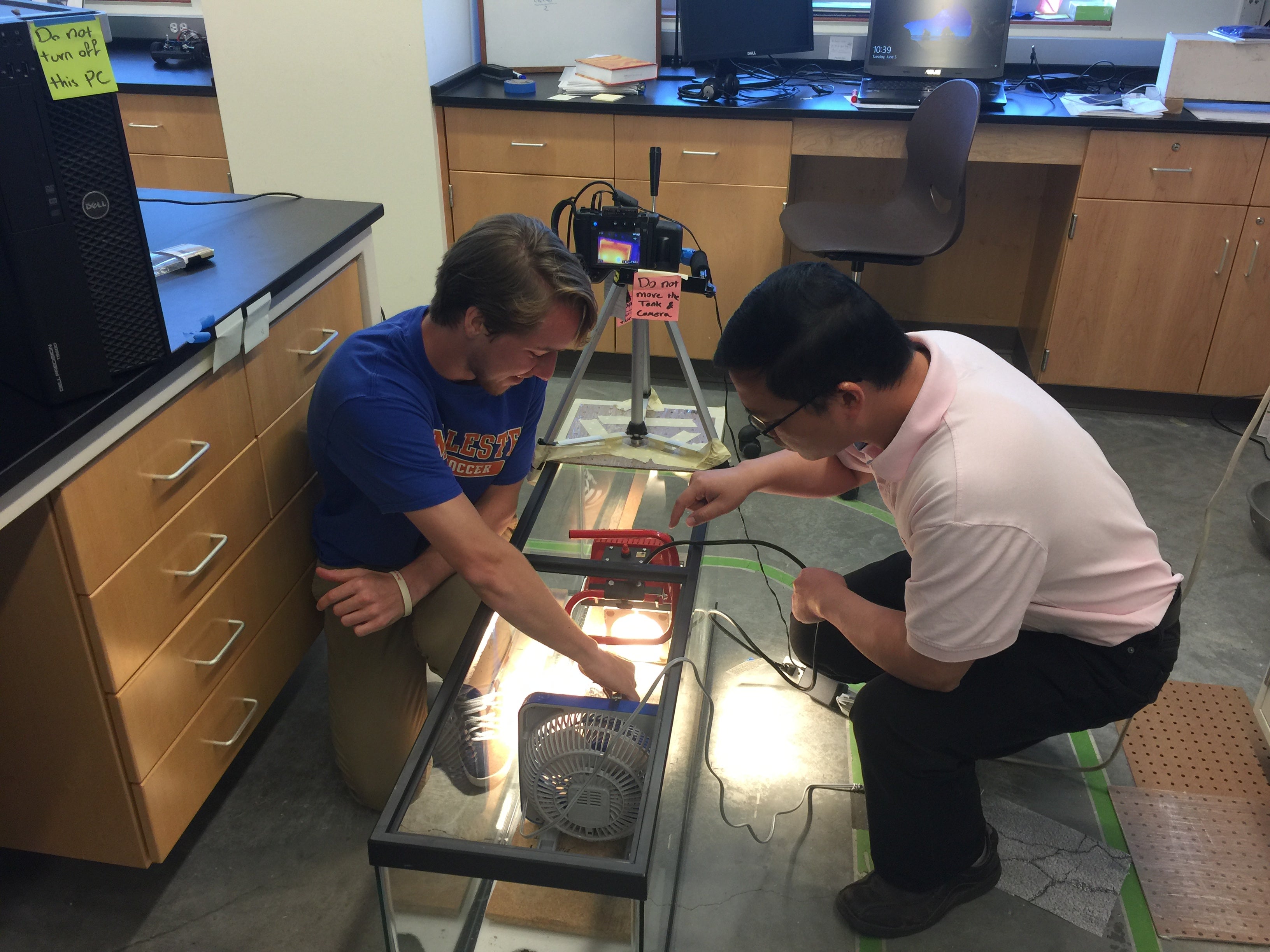
Lu began working with Pitch Aeronautics in 2018 on their project to build an active thermography sensor that would sit neatly on the cyclorotor, all while non-destructively finding fissures and flaws in the infrastructure’s materials.
Thermography is a process in which a material is subjected to heat, while an infrared camera captures images of how the heat flow is, or is not, being conducted through the material. This method makes it possible to detect internal structural damage, such as delamination (or material fracturing), without any destruction.
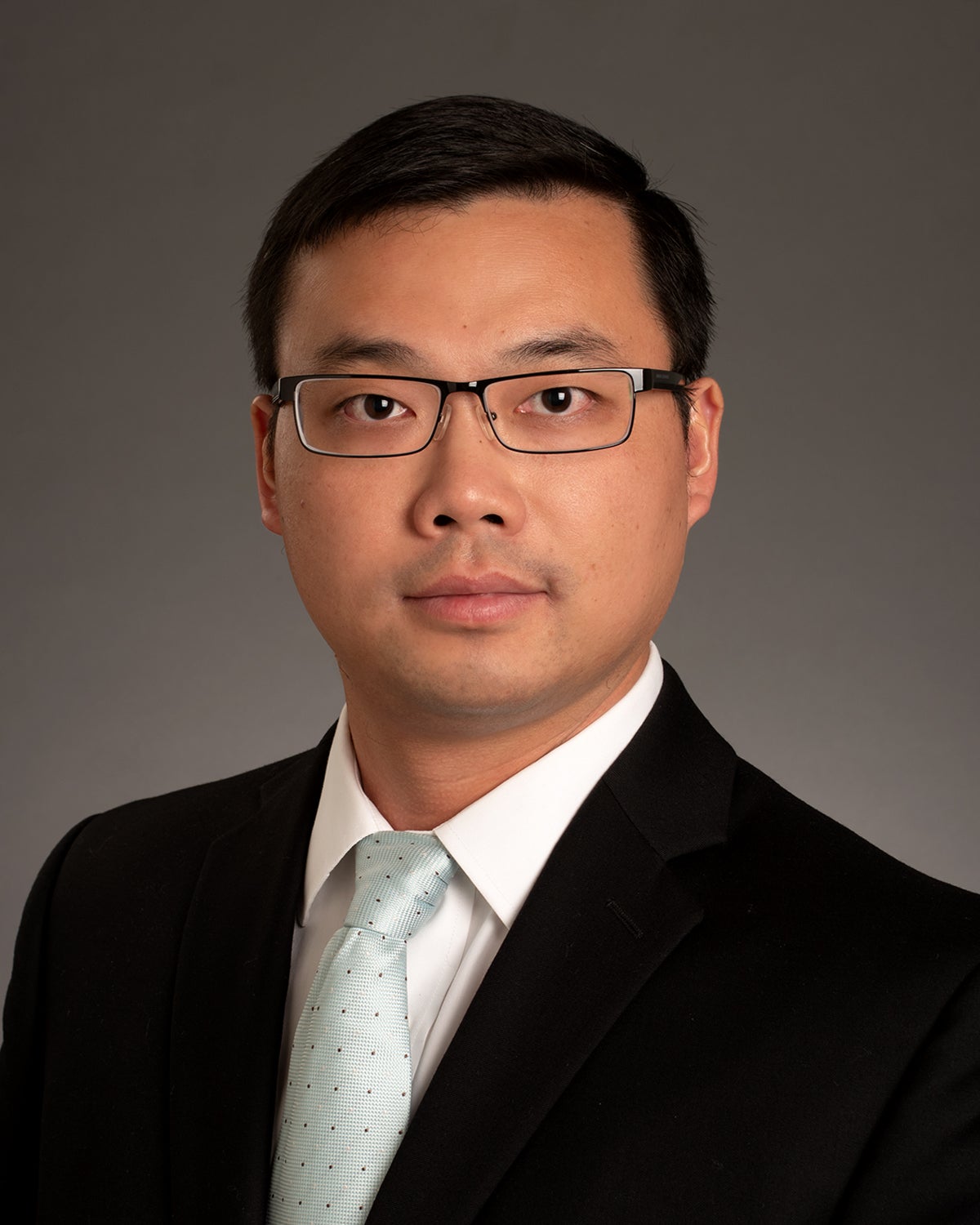
“Steel rebar that’s corroded will expand and create a crack within the concrete. This is called delamination, and because the delamination causes a void, the heat characteristics and heat conductivity are different between the concrete and the void. So therefore, the temperature distribution can be seen and the distribution pattern is an indicator of hidden flaws,” Lu said.
However, Lu takes this thermography to the next level, offering a much more accurate picture and data for further analysis.
“Our innovation is that it is called ‘active’ thermography. Thermography is just taking images, but we have a unique algorithm to correlate the surface temperature distribution with what’s happening underneath,” said Lu.
The sensor will need to be able to heat the inspection subject quite intensely. Lu says that the miniature halogen heat lamp to be used ‘can cook an egg instantly.’
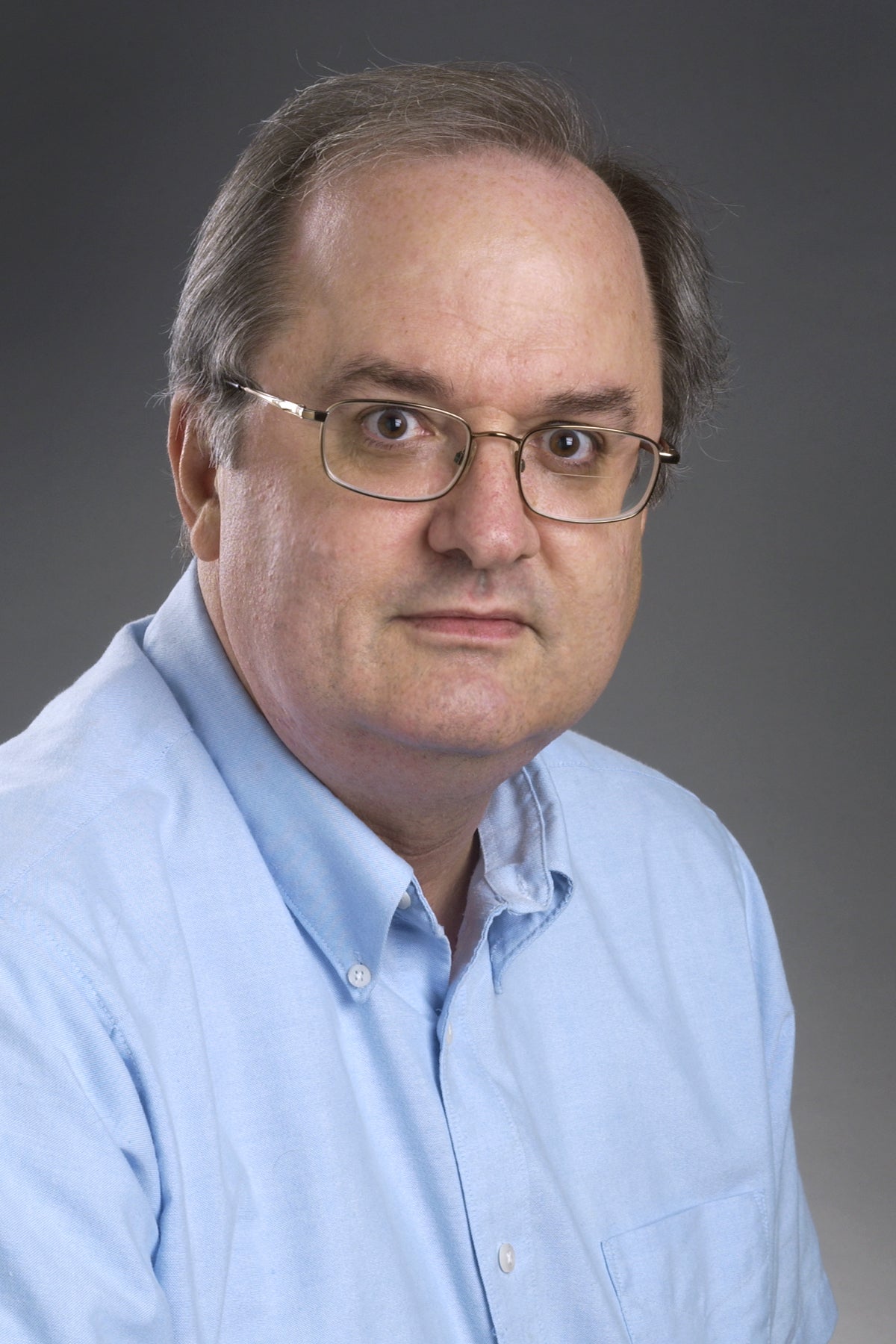
Alongside Lu, electrical and computer engineering associate professor John Chiasson also is supporting the team by working on the control system to guide the cyclorotor’s maneuverability and precision.
This collaboration of university and industry has provided a multitude of opportunities, not only for business and technology development, but also for Idaho institutions to empower one another.
“I enjoy working with students and mentoring them through research projects,” Adams said. “Professor Lu and professor Chiasson have been a pleasure to work with. It’s great to be able to lean on them and leverage their expertise and experience. I expect over the course of the next 18 months it will be rewarding to see the new ideas, team spirit and excitement of flying a new vehicle.”