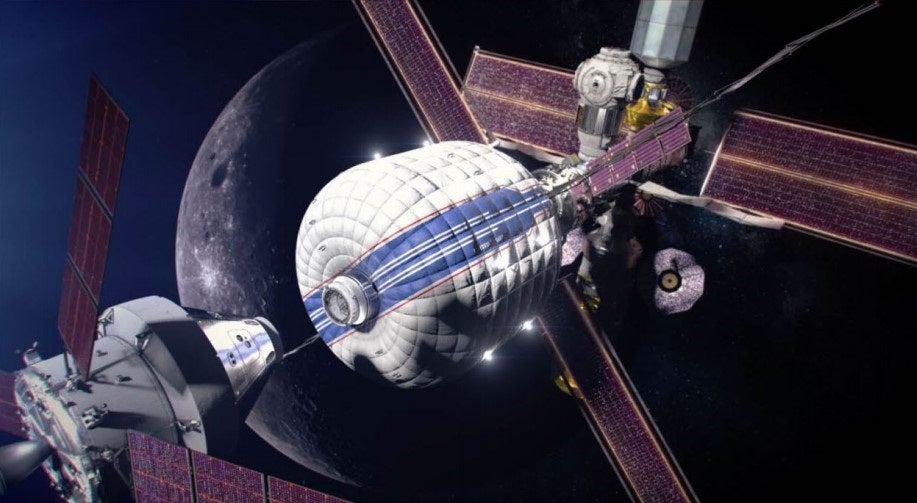
A team from Boise State University and the National Aeronautics and Space Administration (NASA) has developed an approach to monitor the structural health of future inflatable space habitats. Their work was reported in a paper recently published in Nature Partner Journal Flexible Electronics, “Aerosol jet printed capacitive strain gauge for soft structural materials”, and was also recently awarded a U.S. patent (#10512162B2). Led by professor David Estrada of the Boise State College of Engineering, the team demonstrates that low-cost and flexible capacitance based strain gauges can be fabricated with an additive manufacturing technique known as aerosol jet printing (AJP), and outperform commercially available resistance based strain gauges.
The project started as part of NASA Johnson Space Center’s Collaboration for Leveraging Universities in Science, Technology, Engineering, and Research (CLUSTER) program. As part of a Team Based Learning Project in professor Estrada’s Nanoscale Transport course, students were paired with a NASA engineer to identify solutions to real engineering problems faced by the nation’s space program.
Working with NASA Johnson Space Center’s Doug Litteken, the team identified challenges associated with designing structural health monitoring (SHM) systems for inflatable habitat textiles. Litteken’s team had found that resistive strain gauges could not meet the high demands of flexibility, durability, response time, recovery time and sensitivity to strain. Additionally, limitations to developing and deploying this technology are introduced with high-cost of production and complex fabrication processes. The team settled on investigating printed capacitive strain gauges as an alternative technology, and their preliminary data resulted in a two-year contract to further develop the technology.
“Inflatable, expandable, and deployable structures are attractive as habitats for NASA’s deep space missions that test how to live and work safely in harsh environments. The significant benefits of utilizing these structures are their high volume-to-mass ratio, allowing for a large internal volume in a reduced launch package. For long duration missions, it is critical that SHM systems be available to ensure structural life and crew safety,” said Litteken.
AJP technology is a non-contact deposition based on the atomization of nanomaterial inks to form a fine mist or aerosol that is deposited on a substrate. This process eliminates many limitations associated with conventional fabrication methods from its ability to print a wide range of materials such as metal nanoparticles, carbon nanomaterials, functional ceramics, semiconductors, and more. Additionally, device designs are no longer material or geometry limited as AJP can print on a variety of substrates/surfaces, and provides a wide range of feature sizes that span 10 micrometers to five millimeters.
“Strain sensing is utilized for a myriad of applications beyond supporting space exploration missions, and we were very excited to learn that the developments of this study were of interest to the Department of Energy’s Nuclear Energy Office for nuclear sensor applications. The capacitive strain gauges developed in this work demonstrate significant potential for use within nuclear reactors, as the results indicate that they would be better suited for the nuclear reactor environment than their commercial counterparts. The cross-cutting nature of this work demonstrates the significant potential for utilizing additive manufacturing techniques to develop advanced sensing solutions in many different areas,” said Kiyo Fujimoto, lead author on the study. Fujimoto is currently a fifth-year materials science and engineering doctoral student at Boise State.
“This project is an excellent example of how the research and education missions of the university are tightly coupled,“ said Estrada, “What started as an eight-week project in the classroom has resulted in a journal publication, an awarded patent, and continued research funding from two federal agencies. I’m excited about the next steps in the project being led by prof. Ben Johnson in Electrical Engineering, whose team is integrating wireless communications with our sensor. This will be a critical component to realizing a fully automated SHM system, which could have impacts that are out of this world.”
The interdisciplinary study was a collaboration between National Aeronautics Space Administration Johnson Space Center (NASA JSC), Idaho National Laboratory (INL) and spans materials science and engineering, electrical and computer engineering, and mechanical engineering. The work was made possible through resources made available through the Center for Advanced Energy Studies (CAES), the Nuclear Energy Enabling Technologies Advanced Sensors and Instrumentation Program, NASA JSC, the Idaho Space Grant Consortium, and the National Science Foundation.
To learn more, see the team’s research at: Fujimoto, K.T., Watkins, J.K., Phero, T. et al. Aerosol jet printed capacitive strain gauge for soft structural materials. npj Flex Electron 4, 32 (2020). https://doi.org/10.1038/s41528-020-00095-4