Bearing Steels
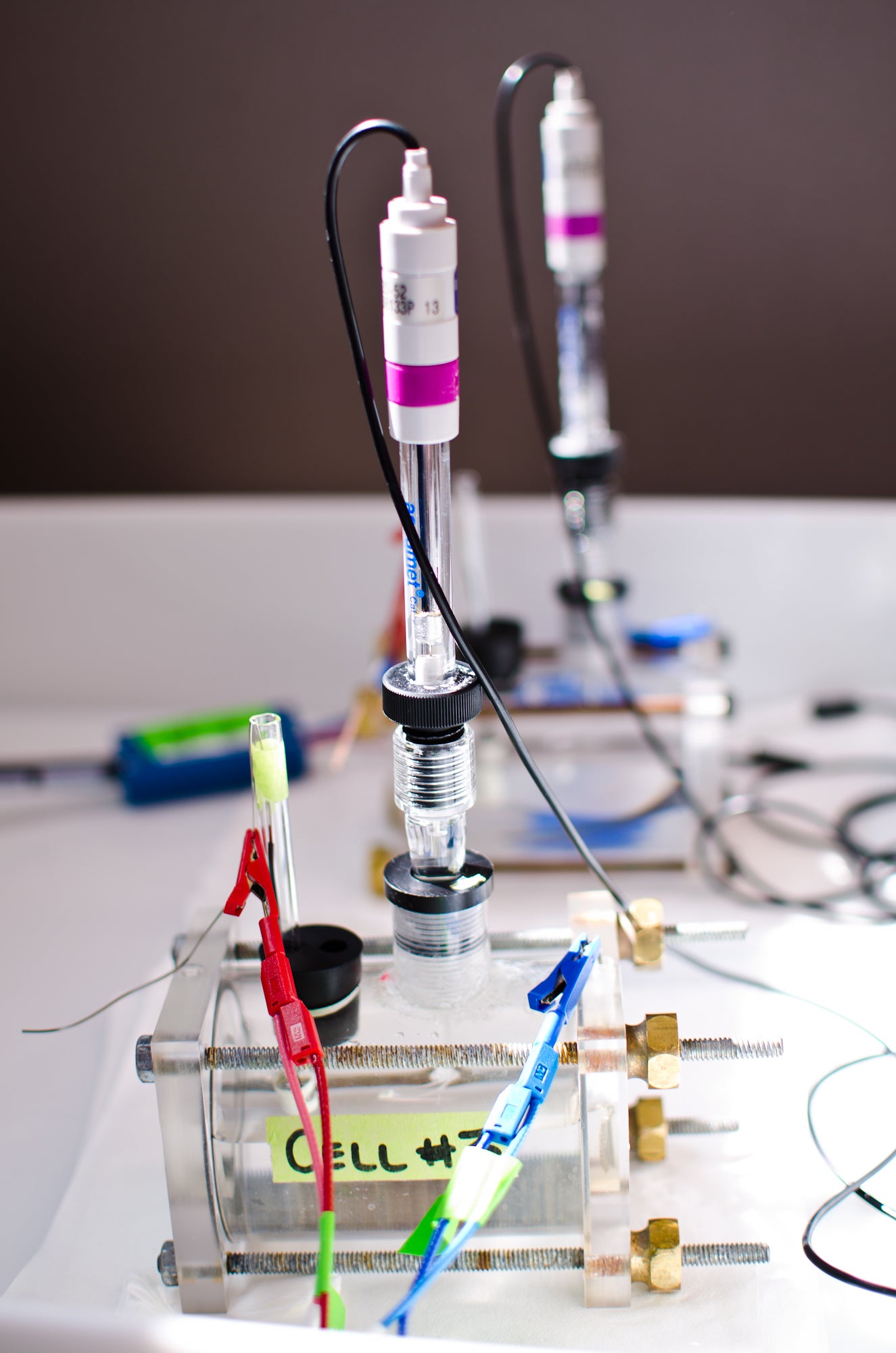
High performance mechanical systems (bearings and gears) in advanced gas turbine engines are required to operate at ever increasing operating, speeds, temperatures and loads. The balance of properties needed for improved bearing steel performance and reliability are typically in conflict with metallurgy requirements. To remain cost-effective, an optimized heat treatment of existing bearing steel compositions is desired. However, premature failure by corrosion pitting is a major concern in aerospace systems especially with operation in marine environments such as an aircraft carrier at sea.
The Bearing Steels project aims to assess the corrosion resistance of candidate heat treatments using a rapid screening test. Electrochemical corrosion testing is performed to rank bearing steel corrosion resistance. Testing is performed on bearing steels with various surface and heat treatments.
Testing for this research utilizes electrochemical impedance spectroscopy (EIS) scans during 24-72 hour immersion in synthetic sea water to provide a way to rapidly screen the corrosion resistance. The primary aim is to determine the effect of surface treatment corrosion behavior of a set of bearing steels that are used in gas turbine engines.
NFSCCS
A significant portion of the Unites States’ annual energy demand is provided by nuclear power. Safe storage of spent nuclear fuel is an essential part of the fuel life-cycle. Currently, spent fuel is typically stored at the reactor site in stainless-steel canisters that are welded shut and back-filled with helium.
Since the storage containers are passively cooled with air from the ambient environment, the canisters may become susceptible to atmospheric induced corrosion damage, particularly in the weld sensitized region. To ensure the integrity of the storage containers, and ensure that prolonged safe-storage is maintained, it is desired to develop a sensor which monitors the possible presence and extent of corrosion damage. Towards this end, we have designed a miniature test apparatus to mimic the conditions in which stress corrosion cracking is likely to occur.
These fixtures use a three point bend test configuration to stress stainless steel samples while collecting resistance measurements over time. Sample failure is signaled by a sudden increase in resistance across the sample. An array of these fixtures, loaded with sacrificial electrodes, are incorporated into the full sensor package. The sacrificial electrodes may be tailored to match the intended material and allow for multiple conditions to be simultaneously monitored. In this manner, the impact of detrimental conditions such as weld sensitization or the presence of residual stress on the corrosion behavior, may be in the sacrificial electrodes and specifically sensed. A corrosion rate or crack propagation rate may also be inferred by sensing failure on progressively larger electrodes. This sensor design can be easily adapted to match a specific metal and allows for multiple corrosion processes to be simultaneously detected.
Scanning Electrochemical Microscopy
The SECM was invented by Allan J. Bard in 1989 where the use of the newly developed ultramicroelectrodes was used in tandem with stepper motors to create a scanning system. The development of the system went on to add a second potentiostat system to the stage of the SECM and subsequent development of the bi-potentiostat. This system can be used in many different modes. Two particular modes of interest are the constant current scanning technique, which can be used to scan the surface of a conductive material, and provide a topographical map of the surface with resolution in the z axis around 100 nm, and the constant voltage scanning technique, which can be used to create a topographical map based on the varying current between the tip and surface of the sample. These techniques can both provide data on how the height of the surface of a material is changing over the entire surface with great detail1.
The SECM has a wide range of use in the material science industry. It can be used for examining the microstructure of a solid or liquid interface, ionic dissolution, electro catalysis, and many other applications. The microscope consists of an ultramicroelectrode that is used as a scanning tip that is brought near the sample to be investigated. The sample itself is set on a stage that also can act as an electrode where different potentials can be applied to the base. These two electrodes are run by a bi-potentiostat that can control independent parameters on each of the electrodes. There is a set of stepper motors as well as piezo motors that can control movement in the x, y, and z directions1. These motors also monitor the location of where the tip of the ultramicroelectrode is in correlation to the stage. You can see the basic setup of an SECM can be seen in Fig. 12.
This instrumentation is used in the corrosion lab to investigate different types of corrosion. The resolution of scanning with the ultramicroelectrode will be utilized to perform local corrosion analysis on various metal systems. This can be used to map local sites for pitting precursors in steel or local corrosion analysis of different heat zones resulting from weld joints. Corrosion of different interfaces such as grain boundaries and inclusions within the metal can also be examined with great detail.