Black phosphorus, which is a stack of multiple layers of atomically thin phosphorene, promises to be a game changer in the world of silicon photonics. Particularly, the functionality of black phosphorus is important in the field of infrared light, which includes applications such as datacom, telecom, Light Detection and Ranging (LiDAR) and sensing. However there is a major challenge facing commercialization of black phosphorus – its production costs can approach 10 times the price of gold.
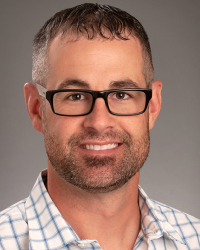
To tackle this challenge, assistant professor Brian Jaques of the Advanced Materials Laboratory and associate professor David Estrada of the Advanced Nanomaterials and Manufacturing Laboratory collaborated with Chad Husko, the founder and CEO of Iris Light Technologies to research mechanochemically synthesized black phosphorus.
Through their collaboration, the team revealed and recently published research that demonstrated the viability of economically converting commodity red phosphorous into optoelectronic grade black phosphorus using a high energy ball milling. The team’s article, titled “Mechanochemical Conversion Kinetics of Red to Black Phosphorus and Scaling Parameters for High Volume Synthesis” was published in Nature partner journal 2D Materials and Applications on Oct. 13, 2020.
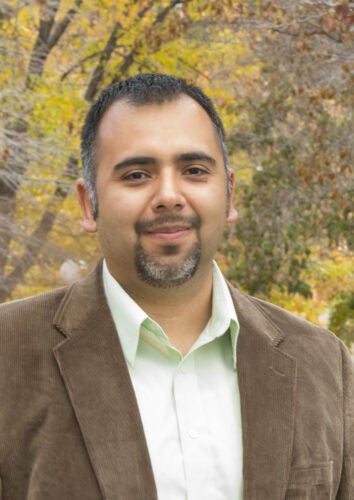
In the research, the team highlighted the use of elemental red phosphorus, an agricultural commodity produced as a byproduct in the manufacturer of phosphate fertilizers. The U.S. alone produces several thousand tons of red phosphorus each year for such applications. Conversely, black phosphorus is produced only in gram quantities by boutique suppliers – a single crystal of black phosphorus produced using a chemical vapor transport route can cost up to $1,000 per gram; in contrast, red phosphorus costs approximately 50 cents per gram.
Using a ball milling conversion route, the researchers hope to reduce the cost of black phosphorus production, as ball mill synthesis excludes the use of expensive and highly toxic chemicals, such as tin iodide, which is used during the vapor transport method. Ideally, black phosphorus will be as inexpensive as $1 per gram.
“Ball milling conversion is the process by which a material is converted into another material using the energy provided through continuous impacts of milling elements using a ball mill,” explained Jaques.
“Understanding and predicting the synthesis, behavior, and capabilities of functional 2D materials is instrumental to any technological advancement. Accordingly, by decreasing the cost of the functional materials and combining their deployment with advanced manufacturing approaches, they become more available to consumers and researchers, which results in further refinement and advancement. The results of this research are profound and could disrupt the communication market in the near future!” said Jaques.
In partnership with Iris Light Technologies Inc., a startup company focused on integrated silicon photonics that was spun out of Argonne National Laboratory, the team further isolated few-layers of this converted black phosphorus and demonstrated photoluminescence emission spanning the near infrared spectrum.
“Scaling a technology is a big challenge, more so when the cost of materials is expensive. This breakthrough already reduces our research and development costs and will accelerate our pathway to market,” said Husko.
Enabling silicon infrared photonics for high speed data transmission could allow a new Moore’s law for optoelectronic device scaling, meaning that it could be possible for the “industry to grow in an compounded way year after year, allowing for us to accomplish communication speeds and bandwidths we can only dream of right now, and it will become more and more affordable,” said Jaques.
With the increase of cloud computing, ubiquitous adoption of the Internet of Things, and the need for higher data throughput, silicon photonics is required to keep up with the huge bandwidth demands. An inexpensive black phosphorus light source will enable commercialization of new optoelectronic devices by means of exploiting atomically thin black phosphorus.
Currently, the group is working towards chemically tailoring black phosphorous to produce electrically pumped lasers on silicon combined with additive manufacturing technologies to integrate the black phosphorus directly onto silicon chips.
“2-dimensional materials are gaining much traction in the field of additive electronics manufacturing,” said Estrada. “Their unique physical properties make them suitable for a wide range of printed and flexible electronics applications. The ability to cheaply synthesize black phosphorus inks for inkjet, aerosol jet, and other printing methods will open up a new design space for printed optoelectronics and allow more researchers to easily enter the field.”
The availability of low-cost black phosphorus for research into silicon photonics has already garnered attention from national labs and industry leaders. An Idaho Global Entrepreneurial Mission (IGEM) grant was awarded to Boise State to fund graduate research, develop intellectual property, and push development efforts. Additionally, Iris Light Technologies, Inc. and Boise State were jointly awarded a Phase 2 STTR contract to support the commercial prototype developments.