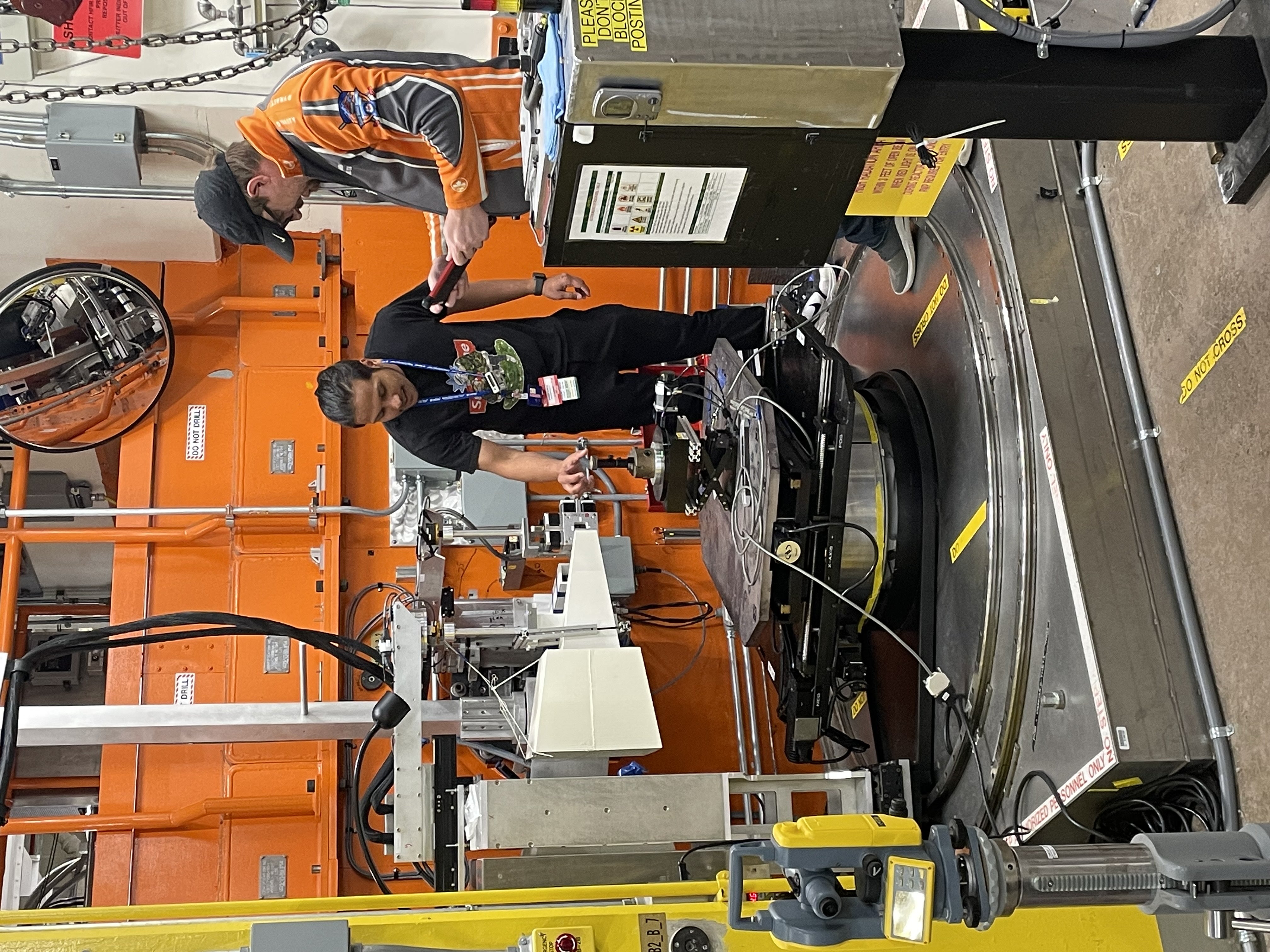
Sandeep Dhakal, a Ph.D. student in the AML, recently traveled to Oakridge National Laboratory (ORNL) to study residual stress in additively manufactured steel at ORNL’s neutron analysis facility. The samples for this experiment were manufactured using laser-wire direct energy deposition (LW-DED) at the ORNL Manufacturing Demonstration Facility (MDF) via the Manufacturing and Materials Joining Innovation Center (Ma2JIC) team (based at the Ohio State University). The wire-laser DED process has a lower resolution than powder-based AM processes; however, the wire feedstock is significantly less expensive than processed AM powder and has a higher deposition rate, making DED more economical and faster than powder-based processes. The unique thermal cycle of AM consists of rapid heating, cooling, and re-melting of underlying layers resulting in the formation of residual stresses in the system. Steep residual stress gradients can result in part distortion and affect the mechanical behavior of materials. Diffraction provides a non-destructive method to study residual stress. Sandeep’s work pairs x-ray diffraction (at CAES) with neutron diffraction (at ORNL), to understand residual stresses both on the surface and within the bulk of the each sample. Three stainless steel samples (a vertical plate, an arc, and a hollow cylinder) were printed and analyzed.
Experiments were conducted at the High Flux Isotope Reactor (HFIR), one of the world’s most advanced neutron scattering research facilities. Beamtime for the instruments is granted through a proposal process and is free of charge with the condition that researchers publish their results. Sandeep’s experiments were conducted at the High Intensity Diffractometer for Residual Stress Analysis (HIDRA) in the HB-2B beamline. This instrument is optimized for strain measurement and determination of residual stress in engineering materials. The high penetrating power of neutrons is ideal for spatial scanning of residual stresses at depths from a millimeter to several centimeters.
At ORNL, Sandeep learned the intricate process that goes into setting up a sample for measurement in the HIDRA instrument, from mounting it to troubleshooting some small errors that might come along the process. He also had the opportunity to see other instruments and learn about ORNL’s capabilities for diffraction, imaging, reflectometry, and spectroscopy as well as their capabilities for irradiation studies.