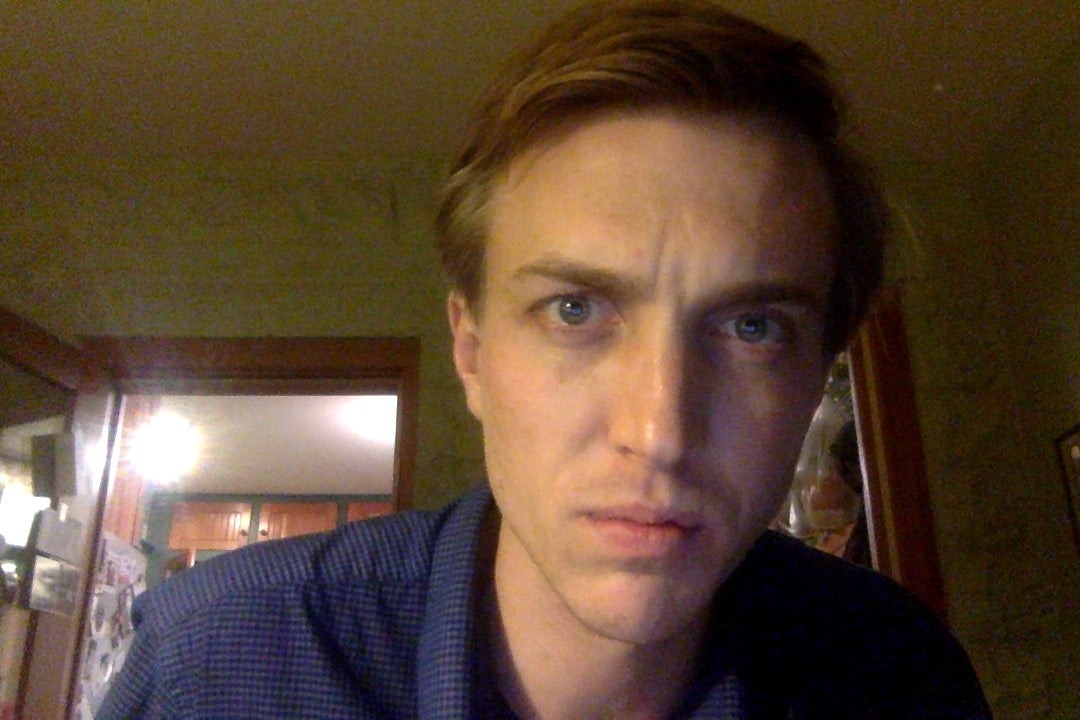
Abstract.
This paper examines the relationship between Boise State University (BSU) and the violence that attends the global garment industry. BSU must take steps to ensure that any clothing bearing the Bronco logo is produced in factories that respect the rights of workers. If BSU is truly committed to ethically produced apparel, it must become an official affiliate of an independent labor-rights monitoring organization known as the Workers Rights Consortium (WRC). I will examine the WRC’s successful record of combating labor rights violations, and conclude this paper by highlighting what BSU stands to gain by becoming an official affiliate of the WRC.
Violence in the Global Garment Industry
On April 23rd, 2013, employees working in the Rana Plaza building in Dhaka, Bangladesh, noticed deep cracks in the walls of the building. Fearing for their safety, workers brought the issue to the attention of the management. Despite the fact that the cracks in the walls “were growing in size; and that [the workers] feared for their lives…the managers replied that anyone refusing to enter the building would have their wages docked, not just for that day but for the entire month” (Hoskin). An engineer named Abdur Razzak Khan was summoned to inspect the cracks in the building. He warned the owner of the building, a man named Sohel Rana, that the building was structurally unsound and recommended immediate evacuation. Khan notified the government and police “issued an evacuation order, but witnesses say that hours before the collapse, Rana told people that the building was safe and garment factory managers told their workers to go inside” (Hossain). On April 24th, 2013, the Rana Plaza building collapsed, killing 1,129 people and severely wounding many more.
While this incident was an undeniable tragedy, the most shocking aspect of the Rana Plaza disaster is how easily it could have been prevented. In an effort to cut costs, Rana Plaza was built out of shoddy materials. It was also constructed illegally, on top of a pond, which meant that the foundation of the building was shaky from the start. This situation was intensified when the owner of the building, Sohel Rana, decided to add an additional three stories to the already existing structure. Mr. Rana leased these new floors to textile manufacturers, despite the fact that the original structure had never been intended to support a factory of any kind. The weight of these new stories, combined with that of the factory machinery, put additional stress on the building. The vibrations from the machinery exacerbated that stress. The end result was an extremely hazardous work environment that culminated in a very preventable catastrophe.
Unfortunately, the Rana Plaza disaster was not an isolated incident. In fact, the collapse of “Rana Plaza was just one…in a series of industrial accidents in Bangladesh’s garment industry, which has become one of the biggest exporters of clothes to the United States and Europe because of its low wages” (New York Times). A year before the Rana Plaza incident, a factory belonging to Tazreen Fashions in Dhaka, Bangladesh, caught fire. 112 people died, and over 200 people were severely injured. As was the case with Rana Plaza, the deaths that resulted from this incident were easily preventable. Most of the people who died in the Tazreen factory fire were “on the first and second floors…and were killed because there were not enough exits” (Bajaj). If basic fire safety regulations had been enforced, either by the owners of the factory or the brands contracting with Tazreen Fashions, there are many people who might still be alive today.
The violence created by the global garment industry is not limited to preventable incidents like the Rana Plaza collapse, or the Tazreen factory fire. In fact, most of the violence that attends the global garment industry is structural in nature. Even now, three years after the Rana Plaza disaster, “workers at the roughly 4,500 factories that form the nucleus of Bangladesh’s enormous garments industry…confront other injustices: unpaid overtime, sexual or verbal abuse, and unsafe and unsanitary working conditions” (D’Almeida and Haq). These workers, 85% of whom are women between the ages of 15 and 25, are overworked and underpaid. According to the International Press Service, 37% of textile workers don’t get sick leave, while 29% don’t get paid maternity leave. Since workers are easy to replace, they are often forced to choose between hazardous, exploitative working conditions and unemployment.
This structural violence persists, in part, because workers who attempt to initiate collective bargaining are subject to threats and physical intimidation. Reforming the garment industry from the inside is difficult because “union busting and other anti-union activity are rampant across the garments sector, with many organisers beaten into submission and scores of others terrorised into keeping their heads down” (D’Almeida and Haq). Factory owners hire thugs to attack or intimidate union leaders and labor activists. In February of 2014, four members of the Bangladesh Federation for Workers Solidarity were attacked, and one was hurt so badly he had to spend the next hundred days in the hospital. Sometimes, troublesome individuals simply disappear. In April of 2012, a labor activist named Aminul Islam was “abducted, tortured and killed…to date his killers have not been found” (D’Almeida and Haq). The culture of fear and intimidation that accompanies the global garment industry makes long-term, meaningful reform exceedingly difficult. Without collective bargaining, it is difficult to secure even basic rights for workers.
BSU and the Global Garment Industry
Boise State University must examine its own position in the global garment industry. With the advance of globalization, the college apparel market is increasingly international in nature. In the college apparel industry, “there is a huge gap between garment-producing people and consumers in…the United States” (Maher, Musiolek and Weber 247). This means that BSU apparel is often produced very far away from Idaho. This distance tends protect the economic structures that abuse workers. The existence of sweatshops is contingent on an “opaque relationship between factory management and labour outsourcing agents” that creates confusion “as to who is responsible for and directly controls wages and working conditions” (Maher, Musiolek and Weber 247). The more complicated the supply chain, the easier it is to defer responsibility when something goes wrong. The complicated structure of the garment industry is the very thing that currently prohibits meaningful reform. So, while untangling the Gordian knot that is the collegiate apparel industry can be both difficult and time consuming, it’s also the only way to encourage corporate accountability. Transparency at every level of the supply chain is a prerequisite to the ethical production of collegiate apparel.
At the very top of the pyramid are “the big brand companies, sports and clothing retailers, big manufacturers, and mail order companies” that “define production orders…decide on deadlines for delivery and settle production prices” (Maher, Musiolek and Weber 246). Brands like Adidas and the VF Corporation purchase a trademark license from BSU, which gives them the right to produce clothing bearing the Boise State logo. In exchange, the university receives a 10% royalty rate. According to information provided by Rachel Bickerton, the Director of Trademark Licensing and Enforcement at Boise State University, these royalties generated $510,852.42 during the 2014-2015 fiscal year. While this might seem like a large sum of money, it pales in comparison to recent years:
Fiscal Years | Total Gross Royalties (July-June) | % of previous FY |
---|---|---|
FY 2008-09 | $559,889.61 | |
FY 2009-10 | $744,190.89 | 133% |
FY 2010-11 | $1,130,847.54 | 152% |
FY 2011-12 | $1,334,903.80 | 118% |
FY 2012-13 | $1,264,246.58 | 95% |
FY 2013-14 | $729,930.44 | 58% |
FY 2014-15 | $510,852.42 (as of Dec 2014) |
This financial information is more than just statistical in nature. It also demonstrates the extent of Boise State’s involvement in the global garment industry. The vast majority of the violence perpetuated by this industry is structural in nature. BSU is implicated in this violence, to the extent that it profits from the current structure. If the BSU logo is worth money, then BSU has an ethical obligation to ensure that the profit this logo generates doesn’t come at the expense of those who make that profit possible. Big brands tend to make a lot of promises when it comes to the issue of ethically-sourced apparel. If Boise State is going to demonstrate its commitment to supply-chain ethics, it needs to do everything in its power to ensure that brands live up to those promises. In other words, BSU must look past the apex of the supply-chain pyramid.
Doing so involves a closer examination of the middle part of BSU’s supply-chain pyramid, which is made up of the “production agencies and supply managers, who search for production sites” (Maher, Musiolek and Weber 246) where brands can produce apparel with the BSU logo. These production agencies are a buffer between the brands that purchase the right to produce BSU apparel and the factories where BSU apparel is produced. Cutting costs wherever possible is the only way these agencies stay in business, since the “production sites employing workers in the garment industry may be quickly dismantled and rebuilt elsewhere on the globe” (Maher, Musiolek and Weber 247). These production agencies serve as middlemen to obfuscate the supply-chain. Since brands deal with production agencies, who often run multiple factories, the brands themselves are one step removed from the production process. In other words, many major apparel companies don’t actually own the factories where their clothing is produced. In fact, clothing for competing brands is often produced in the same factory.
It is important to recognize that the opaque structure of the apparel supply-chain is not incidental. It serves a very strategic purpose: it allows brands to exploit workers and maintain a level of plausible deniability that shields them from the potential (legal, PR) repercussions of that exploitation. When the media discovers a factory violating the rights of workers, big-name brands can claim ignorance. They shift their portion of the blame onto the factory owners and the local government, then argue that the situation is an isolated incident. At that point, preserving the brand’s reputation is simply a matter of cutting ties with the factory in question. It’s easier for brands to cut ties with a factory that’s causing problems than invest time, money and manpower into enforcing its own corporate code of conduct. In the end, the factory is often forced to close. When that happens, the workers are forced to seek employment in other sweatshops—all of which preserves the overall structure of the status quo.
For a university that is quickly developing a reputation as a research institution, such opacity is both intolerable and embarrassing. BSU can no longer allow the brands it contracts with to hide behind these middlemen. It needs a regulatory framework that examines the very bottom of the supply-chain pyramid: the actual factories where the “producers, suppliers, and sub-suppliers receive the orders.” (Maher, Musiolek and Weber 246). If Boise State is going to seek a position in the national spotlight as a leading research institution with a competitive football program, it can not afford to remain ignorant about the factories where its sports apparel is produced. The BSU logo is too valuable to be implicated in “the paradigms of cheap production and mass consumption” that “remain profitable even when labour struggles have led to higher wages in some places” (Maher, Musiolek and Weber 247). If BSU wants to become an internationally renown academic institution, it must be willing to uphold the corresponding ethical obligations that come with its increasingly prevalent position in the globalized economy.
The Workers Rights Consortium
Boise State University must become an affiliate of the Workers Rights Consortium (WRC), an independent labor rights monitoring organization that conducts on-the-ground investigations of factories that produce college apparel. According to its official website, over 182 colleges and universities are currently affiliated with the WRC, including the University of Washington, Arizona State, Cal State Fullerton, Montana State, Gonzaga University, San Diego State, Seattle University, UC Boulder and Washington State. The WRC “does not allow the corporations that are being monitored to participate in its governance structures or financing…it provides a worker-driven process for complaints about noncompliance that includes…remediation plans” (American Federation of Labor 13). In other words, the WRC is free from any potential conflict of interest. It maintains financial independence so that it can honor its commitment to promoting labor-friendly working conditions.
In addition, the Workers Rights Consortium has a proven track record of protecting workers’ rights. In 2009, the WRC issued a detailed report that accused Russell Athletics of closing down the Jerzees de Honduras factory in response to workers’ attempts to organize. When Russell Athletics ignored the report, 57 colleges and universities around the country terminated their contracts with the brand. Russell Athletics had no choice but to rehire “1,200 workers in Honduras who lost their jobs when Russell closed their factory soon after the workers had unionized” (Greenhouse). The WRC’s commitment to transparency made it impossible for Russell Athletics to sweep the issue under the rug. The incident set a valuable precedent, and demonstrates the WRC’s willingness to hold brands accountable when those brands violate the rights of workers.
Other WRC victories are more recent. In 2014, two union leaders in Bangladesh were hospitalized after being assaulted outside a garment factory owned by the Azim Group. The Azim Group, which employs 27,000 workers in 24 different factories, claimed that the assaults were the work of private individuals and had nothing to do with the victim’s union affiliations. The WRC investigated the incident and found “testimonial and videographic evidence…that Azim Group carried out a coordinated series of attacks on leaders of the Global Garments Ltd. Union… involving numerous intentional acts of violence and public humiliation” (Workers Rights Consortium). The report generated international attention; many major brands began to pressure the Azim Group to demonstrate a stronger commitment to worker rights. In 2015, the Azim Group “agreed to stop efforts to oust a labor union, to pay the medical bills of a badly beaten union leader and to allow several union officials to return to work with full back pay” (Greenhouse and Tabuchi). This success was made possible by the fact that the WRC offers the college apparel industry a meaningful framework for reform.
This framework emphasizes cooperation—not confrontation—with the brands that produce college apparel. Many colleges and universities around the country are affiliates, so most big-name brands already have a working relationship with the WRC. These brands know that the WRC is not interested in destroying their reputation. When the WRC identifies problems with a factory, it gives the brand an opportunity to reform that factory before issuing a public report. In many instances, the WRC can say that the labor violations have already been addressed when it publishes its public report of those violations. In other words, the increased transparency and accountability provided by the WRC disincentivizes the “cut-and-run” approach that reshuffles the existing structure of the sweatshop industry without changing how it operates.
The Cost and Benefits of Becoming a WRC Affiliate
Affiliating with the WRC isn’t free, but it is inexpensive. To become an affiliate of the WRC, Boise State University would be required to pay 1% of the previous year’s gross licensing revenue as an annual affiliation fee. This means that, if Boise State were to affiliate with the WRC for the 2015-2016 fiscal year, it would cost the university a total of $5,108. Since the affiliation fee is a flat 1% of the revenue generated by the bookstore, the actual monetary amount BSU would pay each year is subject to some degree of fluctuation. During the 2012-2013 fiscal year for example, the BSU bookstore generated $1,334,903.80 in gross royalties. WRC affiliation for the following 2013-2014 school year would have cost the university approximately $13,349.04. While this amount might seem substantial, it is a drop in the bucket compared to the true monetary value of the Bronco logo.
Opponents of the WRC will undoubtedly argue that the cost of affiliation places a burden on the student body, since the revenue that the bookstore generates currently goes towards scholarships. While affiliating with the WRC would cost the university anywhere between $5,000 – $15,000 every year, this figure pales in comparison to the whopping $13 million that BSU spent on scholarships and fellowships during the 2014-2015 school year. Considered in this context, the cost of affiliating with the WRC would be little more than a pittance. For the cost of a used car, BSU can protect the reputation of the Bronco logo and ensure that the clothing sold in the bookstore is produced in factories that respect the rights of workers. When analyzed from this angle, the expenditure is more than a bargain—after all, can you really put a price on doing the right thing?
There are also indirect benefits to joining the WRC that must be taken into consideration. If Boise State University were to become a WRC affiliate, it would be the first university in Idaho and the first university in the Mountain West Conference to do so. This would allow BSU to assume a position of regional leadership with regard to the issue of supply-chain ethics. In addition, since 80% of tier 1 research institutions are currently members of the WRC, affiliating with the WRC would help Boise State establish a positive association with big-name research institutions like Columbia and Duke. These are intangible benefits, in that they’re difficult to translate into monetary terms. Nevertheless, they represent a valuable series of public relations opportunities for BSU, and could help the university broaden its sphere of influence. In other words, affiliating with the WRC is more than just a demonstration of BSU’s commitment to integrity and transparency: it is also a valuable investment opportunity for the university that should not be neglected or taken for granted.
Works Cited
“Affiliate Schools.” WRC. Workers Rights Consortium, n.d. Web. 26 Apr. 2015.
Anner, Mark. “The Limits of Voluntary Governance Programs: Auditing Labor Rights in the Global Apparel Industry.” (2013): n. pag. School of Labor and Employment Relations. Pennsylvania State University, Dec. 2013. Web. 26 Apr. 2015.
“Bangladesh Factory Collapse Blamed on Swampy Ground and Heavy Machinery”.” The Guardian. Associated Press, May 2013. Web. 26 Apr. 2015.
Bajaj, Vikas. “Fatal Fire in Bangladesh.” The New York Times, 25 Nov. 2012. Web. 10 Mar. 2016.
Bickerton, Rachel. “Licensee Information.” Message to the author. 7 Apr. 2015. E-mail.
“Commercial Merchandise – Office of Trademark Licensing and Enforcement.” Office of Trademark Licensing and Enforcement. Boise State University, n.d. Web. 26 Apr. 2015.
D’Almeida, Kanya, and Naimul Haq. “Rights Abuses Still Rampant in Bangladesh’s Garment Sector.” Rights Abuses Still Rampant in Bangladesh’s Garment Sector. Inter Press Service, 22 Apr. 2015. Web. 26 Apr. 2015.
Duncan, Maxim, and Clare Jim. “Foxconn China Plant Closed after 2,000 Riot.” Reuters. N.p., 24 Sept. 2012. Web. 26 Apr. 2015.
Facts and Figures. Digital image. Boise State University. Communications & Marketing, 2015. Web. 26 Apr. 2015.
“FAQ.” Feminists Against Sweatshops. Feminist Majority Foundation, n.d. Web. 26 Apr. 2015.
Finnegan, Brian. “Responsibility Outsourced: Social Audits, Workplace Certification, and Twenty Years of Failure to Protect Worker Rights.” (2014): n. pag. AFLCIO. The American Federation of Labor, 1 Aug. 2014. Web. 26 Apr. 2015.
Frequently Asked Questions – FAQ. Workers Rights Consortium, n.d. Web. 10 Mar. 2016.
Greenhouse, Steven, and Hiroko Tabuchi. “Company in Bangladesh Agrees to Union Peace.” The New York Times. The New York Times, 18 Feb. 2015. Web. 26 Apr. 2015.
Greenhouse, Steven. “Labor Fight Ends in Win for Students.” The New York Times. The New York Times, 17 Nov. 2009. Web. 26 Apr. 2015.
Greenhouse, Steven. “Union Leaders Attacked at Bangladesh Garment Factories, Investigations Show.” International Business. The New York Times, 22 Dec. 2014. Web. 26 Apr. 2015.
Hoskins, Tansy. “Op-Ed | Preventing Another Rana Plaza.” The Business of Fashion. N.p., 16 Sept. 2013. Web. 26 Apr. 2015.
Hossain, Farid. “Bangladesh Building-collapse Death Toll Tops 600.” Washington Post. The Washington Post, 5 May 2013. Web. 26 Apr. 2015.
“Interm Summary Report: Third Party Complaint Regarding Hermosa Manufacturing.” Cornell School of Industrial and Labor Relations. Fair Labor Association, 2006. Web. 26 Apr. 2015.
Johnson, Angus. “USAS Powers Ahead!” Student Activism. N.p., 01 May 2009. Web. 26 Apr. 2015.
“Mission & Charter.” Fair Labor Association, 12 Feb. 2014. Web. 26 Apr. 2015.
Musiolek, Bettina, and Sam Maher. “False Promises and Movements of Contestation in the Global Garment Industry.” Migration, Precarity, & Global Governance: Challenges and Opportunities for Labour. By Anna Weber. N.p.: Oxford UP, 2015. 245-60. Print.
“New IPhone, Old Abuses: Have Working Conditions at Foxconn in China Improved?” SACOM. Students & Scholars Against Corporate Misbehavior, 20 Sept. 2012. Web. 26 Apr. 2015.
Nova, Scott, and Isaac Shapiro. “Polishing Apple: Fair Labor Association Gives Foxconn and Apple Undue Credit for Labor Rights Progress.” Economic Policy Institute, 8 Nov. 2012. Web. 26 Apr. 2015.
“One Year After Rana Plaza.” The New York Times. The Editorial Board, 27 Apr. 2014. Web. 26 Apr. 2015.
Supriadi, Ahmad. “Public Statement.” Letter. 19 Oct. 2012. MS. Indonesia, Tangerang, Banten.
Taber, Rachel. “WRC Materials.” Message to the author. 15 Apr. 2015. E-mail.
“WRC Memorandum.” Workers Rights Consortium, 18 Dec. 2014. Web. 26 Apr. 2015.