Betsy Rosales, Dr. Zhangxian Deng, Dr. Benjamin C. Johnson
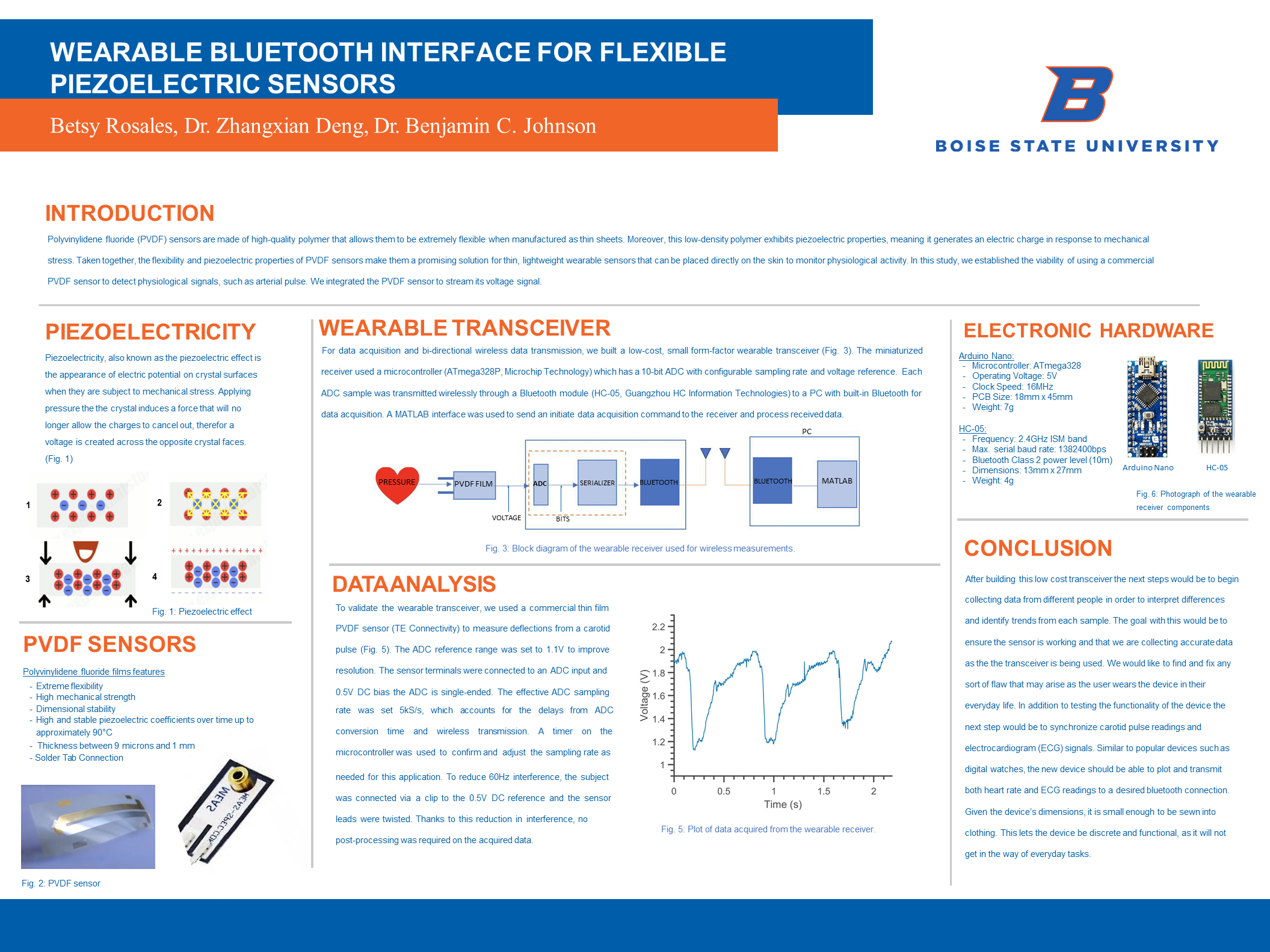
Introduction
Polyvinylidene fluoride (PVDF) sensors are made of high-quality polymer that allows them to be extremely flexible when manufactured as thin sheets. Moreover, this low-density polymer exhibits piezoelectric properties, meaning it generates an electric charge in response to mechanical stress. Taken together, the flexibility and piezoelectric properties of PVDF sensors make them a promising solution for thin, lightweight wearable sensors that can be placed directly on the skin to monitor physiological activity. In this study, we established the viability of using a commercial PVDF sensor to detect physiological signals, such as arterial pulse. We integrated the PVDF sensor to stream its voltage signal.
Piezoelectricity
Piezoelectricity, also known as the piezoelectric effect is the appearance of electric potential on crystal surfaces when they are subject to mechanical stress. Applying pressure the the crystal induces a force that will no longer allow the charges to cancel out, therefor a voltage is created across the opposite crystal faces. (Fig. 1)
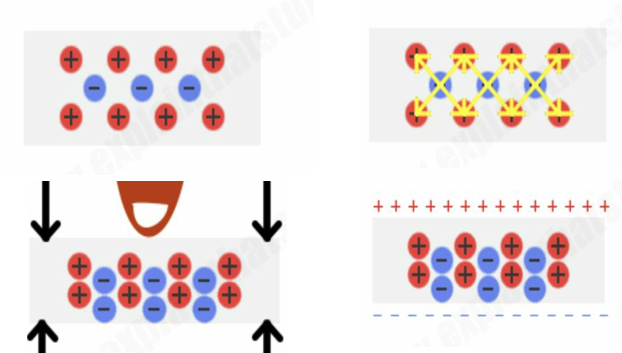
PVDF Sensors
Polyvinylidene fluoride films features
- Extreme flexibility
- High mechanical strength
- Dimensional stability
- High and stable piezoelectric coefficients over time up to approximately 90°C
- Thickness between 9 microns and 1 mm
- Solder Tab Connection
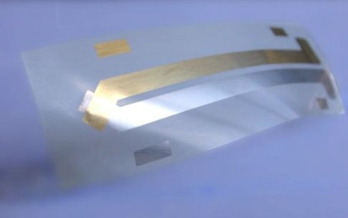
Wearable Transceiver
For data acquisition and bi-directional wireless data transmission, we built a low-cost, small form-factor wearable transceiver (Fig. 3). The miniaturized receiver used a microcontroller (ATmega328P, Microchip Technology) which has a 10-bit ADC with configurable sampling rate and voltage reference. Each ADC sample was transmitted wirelessly through a Bluetooth module (HC-05, Guangzhou HC Information Technologies) to a PC with built-in Bluetooth for data acquisition. A MATLAB interface was used to send an initiate data acquisition command to the receiver and process received data.
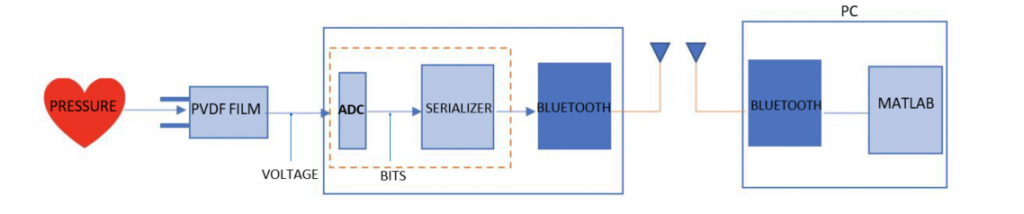
Data Analysis
To validate the wearable transceiver, we used a commercial thin film PVDF sensor (TE Connectivity) to measure deflections from a carotid pulse (Fig. 5). The ADC reference range was set to 1.1V to improve resolution. The sensor terminals were connected to an ADC input and 0.5V DC bias the ADC is single-ended. The effective ADC sampling rate was set 5kS/s, which accounts for the delays from ADC conversion time and wireless transmission. A timer on the microcontroller was used to confirm and adjust the sampling rate as needed for this application. To reduce 60Hz interference, the subject was connected via a clip to the 0.5V DC reference and the sensor leads were twisted. Thanks to this reduction in interference, no post-processing was required on the acquired data.
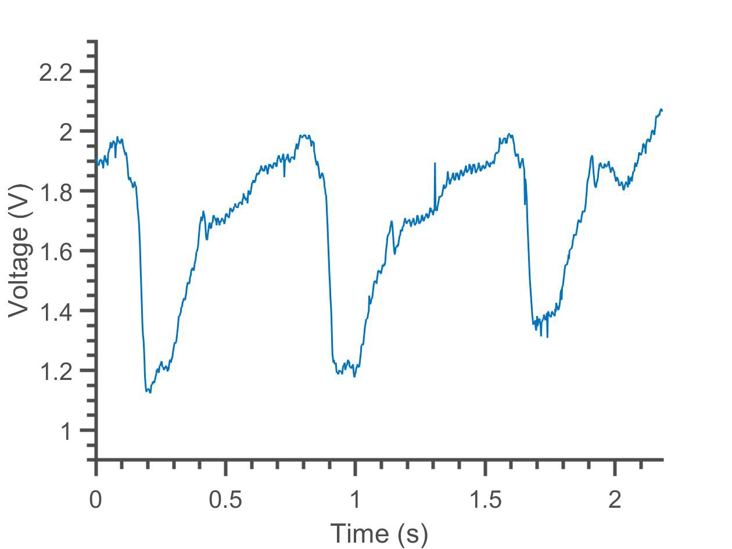
Electronic Hardware
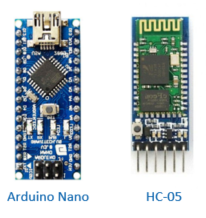
Arduino Nano:
- Microcontroller: ATmega328
- Operating Voltage: 5V
- Clock Speed: 16MHz
- PCB Size: 18mm x 45mm
- Weight: 7g
HC-05:
- Frequency: 2.4GHz ISM band
- Max. serial baud rate: 1382400bps
- Bluetooth Class 2 power level (10m)
Conclusion
After building this low cost transceiver the next steps would be to begin collecting data from different people in order to interpret differences and identify trends from each sample. The goal with this would be to ensure the sensor is working and that we are collecting accurate data as the transceiver is being used. We would like to find and fix any sort of flaw that may arise as the user wears the device in their everyday life. In addition to testing the functionality of the device the next step would be to synchronize carotid pulse readings and electrocardiogram (ECG) signals. Similar to popular devices such as digital watches, the new device should be able to plot and transmit both heart rate and ECG readings to a desired bluetooth connection. Given the device’s dimensions, it is small enough to be sewn into clothing. This lets the device be discrete and functional, as it will not get in the way of everyday tasks.
Additional Information
For questions or comments about this research, contact Betsy Rosales at betsyrosales@u.boisestate.edu.